Załadunek szyty na miarę
Kopalnia Melafiru Tłumaczów posiada jeden z najnowocześniejszych procesów technologicznych załadunku i układów transportu kruszywa w Polsce. Zaprojektowanie i wykonanie całkowicie zautomatyzowanej załadowni wraz z systemem taśmociągów było nie lada wyzwaniem, jednak cel został całkowicie osiągnięty.
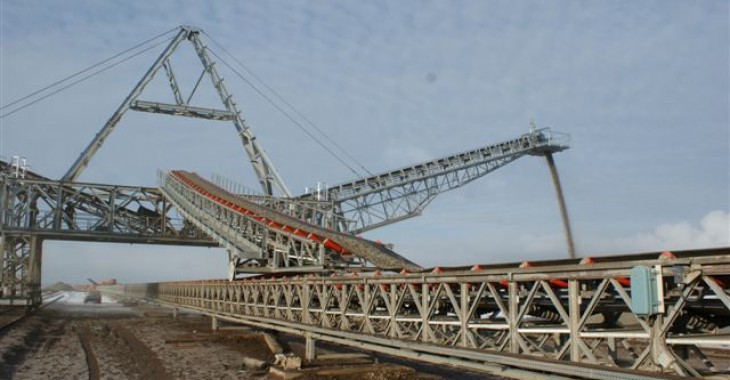
Urzeczywistnić wizję inwestora
Proces technologiczny w powstającej najnowocześniejszej kopalni kruszywa – od zasypu kosza na pierwszym stopniu kruszenia aż do załadunku wagonów – miał być całkowicie zautomatyzowany i pozbawiony jakichkolwiek zbędnych operacji. W pierwotnych założeniach transport kruszywa ze stożków gotowych produktów umieszczonych bezpośrednio przy zakładzie stacjonarnym, odbywać się miał za pomocą trzech przenośników sprowadzających materiał na bocznicę kolejową i być ładowany na wagony przy użyciu kosza załadunkowego. Takie rozwiązania ograniczały możliwości produkcyjne zakładu, wymuszając sprzedaż tych frakcji, które blokowały stożki produktu przy zakładzie stacjonarnym, a czas załadunku wagonów był znacznie dłuższy niż obecnie.
Zadanie te było olbrzymim wyzwaniem – zaprojektować składowisko zastępcze gotowych produktów, z w pełni zautomatyzowanym procesem obsługi magazynowania, transportu, dozowania i załadunku gotowych frakcji na wagony. Zespół projektantów naszej firmy pod kierunkiem pana Pawła Woryny, przy wsparciu RDK Projekt (odpowiedzialni za prace budowlane i pozwolenia) oraz HTS Projekt (automatyzacja i elektryfikacja) przystąpił do prac projektowych, mających na celu urzeczywistnienie wizji inwestora.
Pełna automatyzacja
Pierwszym elementem łączącym linię transportu kruszywa z projektowanym magazynem był przesyp kierunkowy, umożliwiający załadunek wagonów kruszywem bezpośrednio spod stożków produktów przy zakładzie stacjonarnym lub skierowanie ich na zwałowarkę obsługującą składowisko zastępcze. Magazyn został zaprojektowany w oparciu o dwa stalowe tunele, każdy długości 240 metrów, wyposażone w 32 rynny wibracyjne, po dwie dla każdego z boksów. Tunele zostały oddalone od siebie o 60 metrów i umieszczono między nimi zwałowarkę, która miała możliwość zasypu na całej długości składowiska po obu jego stronach. Magazyn posiada 16 boksów, w których można składować różnego rodzaju produkty (podział został wykonany za pomocą prefabrykowanych elementów betonowych, tzw. „tetek”). Zabieg ten dał możliwość składowania 260 tysięcy ton różnego rodzaju gotowych produktów. Oba tunele zostały wyposażone w przenośniki taśmowe wybierające, które przekazują materiał na przenośniki odstawy, na bocznicę kolejową.
Cały proces załadunku obsługiwany, kontrolowany i monitorowany jest ze stanowiska sterowania, umieszczonego przy bocznicy kolejowej. Sterujący procesem załadunku wybiera sposób i ilość załadunku na wybrane wagony. Cała reszta odbywa się automatycznie.
Fot. Budkrusz Sp. z o. o.
Cały materiał znajdą Państwo w magazynie "Surowce i Maszyny Budowlane" 1/2014