Wiercenie XXI w.
Nowoczesna kopalnia odkrywkowa to taka, która bazuje na zdalnym sterowaniu i kontroli pracy maszyn oraz innowacyjnych sposobach nawigacji, które są kluczem do sukcesu związanego z robotyzacją wydobycia kopalin. Rozwiązania takie z powodzeniem wprowadzono już do ładowarek i wozów odstawczych w kopalniach pod ziemią oraz do wiertnic pracujących w kopalniach odkrywkowych.
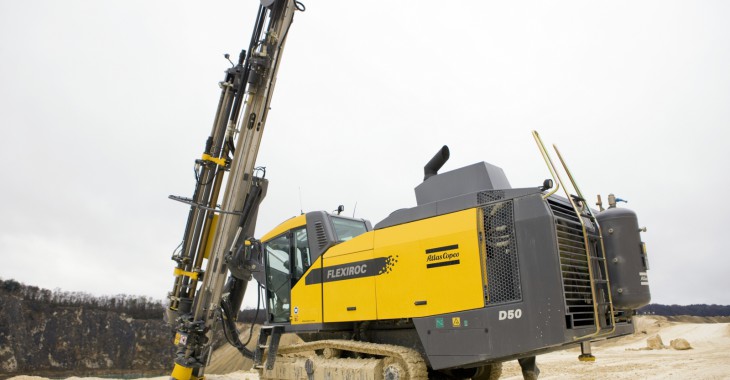
Stale poszukuje się coraz lepszych i wydajniejszych metod pozyskiwania surowców zalegających w skałach trudnourabialnych (rudy metali, budowlane i chemiczne surowce mineralne). Odpowiedź na pytanie, czy istnieje sposób rozbudowy lub wręcz budowy nowej kopalni, który pomoże w redukcji kosztów pozyskiwania surowca nie jest łatwa. Dla inżynierów zaangażowanych w budowę korytarzy, chodników, przekopów (ale także i tuneli) priorytetem jest niezwykle precyzyjne wiercenie mało średnicowych (38÷45 [mm]) krótkich otworów poziomych [12,13, 14,16,17,19], natomiast dla inżynierów górników wyzwaniem jest osiągnięcie wysokiej precyzji w drążeniu długich średnio średnicowych (89÷127 [mm]) otworów pionowych w spągu lub w stropie [6][10]. Te dwa aspekty niezwykle wpływają na koszt produkcji surowca, w której tym sposobem eliminuje się do minimum możliwość powstawania brył nadwymiarowych, których konieczność rozdrobnienia wymaga zaangażowania dodatkowego czasu i środków technicznych.
Wydaje się, że w obecnie pojawiły się czynniki mogące mieć daleko idące konsekwencje dla rozwoju kopalń, tj. ostatnie postępy w zdalnym sterowaniu, automatyzacji pracy i nawigacji ciężkimi maszynami roboczymi, w których zagadnienie ręcznego sterowania doprowadzono właściwie do perfekcji, stosując w układach sterowania joysticki hydrauliczne i elektrohydrauliczne [5,15,18]. Automatyzacja, zdalne sterowanie i nawigowanie tymi maszynami jest w przypadku eksploatacji surowców zalegających w wyżej wzmiankowanych skałach bardzo trudne, przede wszystkim z uwagi na cykliczność, ale i wymaganą kolejność prowadzonych prac z tym związanych: • wiercenie otworów strzałowych (wozy wiertnicze, wiertnice), • strzelanie z użyciem MW, • załadunek i transport (ładowarki, koparki), • kotwienie (na odkrywce nie) stropu.
W dalszej części artykułu zaprezentowano tylko ogólne zasady wprowadzania automatyzacji i fragmenty rozwiązań, których wprowadzenie zakończyło się sukcesem. Artykuł odnosi się do wybranych maszyn wiertniczych związanych z eksploatacją z pomocą MW grupy surowców zalegających w skałach zwięzłych i bardzo zwięzłych nie tylko na powierzchni, ale i pod ziemią.
Motywy wprowadzania zdalnego sterowania maszynami roboczymi
Spiritus movens działań stojących za decyzjami inwestycyjnymi w automatyzację są przede wszystkim takie aspekty, jak: • Ekonomia – umożliwiająca uzyskanie oszczędności w kosztach wydobycia surowca, co zwiększa konkurencyjność konsorcjum wydobywczego na rynku. • Bezpieczeństwo – w centrum którego jest minimalizacja ryzyka pracy górników w niezwykle trudnym, nieprzyjaznym i niebezpiecznym środowisku pracy. • Ergonomia – pozwalająca na stwarzanie operatorom coraz bardziej przyjaznych i komfortowych warunków pracy. • Jakość – wyrażająca się takimi czynnikami, jak: dokładne wykonywanie otworów wiertniczych wyznaczonych przez metrykę wiertniczą skutkujące lepszą fragmentacją urobku, ale i uzyskiwaniem wyrobisk o pożądanym w technologii wydobycia kształcie (mniejsze straty urobku), stabilne cykle odbioru i transportu urobku ładowarkami pozwalające na większą kontrolę nad ilością urobku z każdego przodka itp. • Wydajność – która jakkolwiek jest podstawą mechanizacji wszelkich prac, i która powinna być zwiększona w poprawnie zrealizowanym nowym rozwiązaniu, tym niemniej w początkowych fazach każdego nowego projektu dotyczącego automatyzacji procesu wydobycia nie jest ona najważniejszą.
Systemy sterowania i kontroli pracy maszyn roboczych
Odmienność systemów eksploatacji surowców zalegających w skałach zwięzłych i bardzo zwięzłych a eksploatowanych metodą odkrywkową lub podziemną spowodowała, że w technice, w szczególności w technice nawigacji maszynami roboczymi, wykształciły się nieco odmienne systemy odczytu i sterowania położeniem maszyn, a także sterowania ich funkcjonowaniem. Analizując rozwiązania związane ze zdalnym sterowaniem i nawigacją maszynami roboczymi, można je przyporządkować czterem głównym grupom: • zdalne sterowanie maszyną będącą w zasięgu wzroku (line of light): operator musi widzieć urządzenie, którym steruje (fot. 1), • zdalne sterowanie z użyciem kamer i monitorów, • telesterowanie, • praca programowa – autonomiczna.
Sterowanie line of light
System sterowania maszyną będącą w polu widzenia operatora oparty jest na urządzeniu składającym się z dwóch oddzielnych jednostek (hardware): • jednostka RRC (Radio Remote Control) znajdująca się po stronie operatora i posiadająca wszystkie kontrolery i wskaźniki,
• jednostka zamontowana w maszynie, zintegrowana z elektrohydraulicznym systemem sterowania maszyną.
Najważniejszą zaletą tego systemu jest dwukierunkowa łączność (radiowa) między pilotem a odbiornikiem. Oprócz przekazywania komend sterujących z pilota do maszyny, możliwa jest transmisja danych z maszyny do pilota sterującego. Pozwala to na sprawdzanie stanu maszyny bez konieczności zbliżania się do niej (fot. 1, fot. 2). W zależności od potrzeb i sytuacji sterowanie maszyną może być zdalne lub lokalne. Zdalne sterowanie jest realizowane drogą radiową lub kablową. Sterowanie lokalne maszyną odbywa się za pośrednictwem pilotów kablowych połączonych bezpośrednio ze sterownikiem maszyny (z pominięciem odbiornika radiowego). Większość użytkowników woli jednak stosować między tymi jednostkami systemu komunikację bezprzewodową, jakkolwiek wytwórcy oferują również możliwość komunikacji przewodowej. Zaletą rozwiązania kablowego jest to, że jednostka sterująca może być zasilana z urządzenia kontrolowanego. Urządzenia ze sterowaniem line of light zostały przez wielu wytwórców poddane procedurze standaryzacji obejmującej rozwiązania rozmieszczenia joysticków, wskaźników i przycisków na panelu jednostki RRC. Dotyczy to również rozwiązań obejmujących specyfi czne w swej konstrukcji i działaniu maszyny wiertnicze wyposażane w nowej generacji w system kontroli pracy przewodu wiertniczego RCS (Rig Control System), gdzie stosuje się przejrzysty i prosty w obsłudze interfejs magistrali CAN (Controller Area Network) komunikacji jednostki umieszczonej na urządzeniu sterowanym z jednostką sterującą RRC. Informacje o pozycji drążka sterującego joysticka, przyciskach, wyłącznikach i alarmach przesyłane są w formie szeregowych pakietów danych magistralą do wiertnicy.
Cały artykuł znajduje się w magazynie "Surowce i Maszyny Budowlane" 2/2015